Loading 3D model...
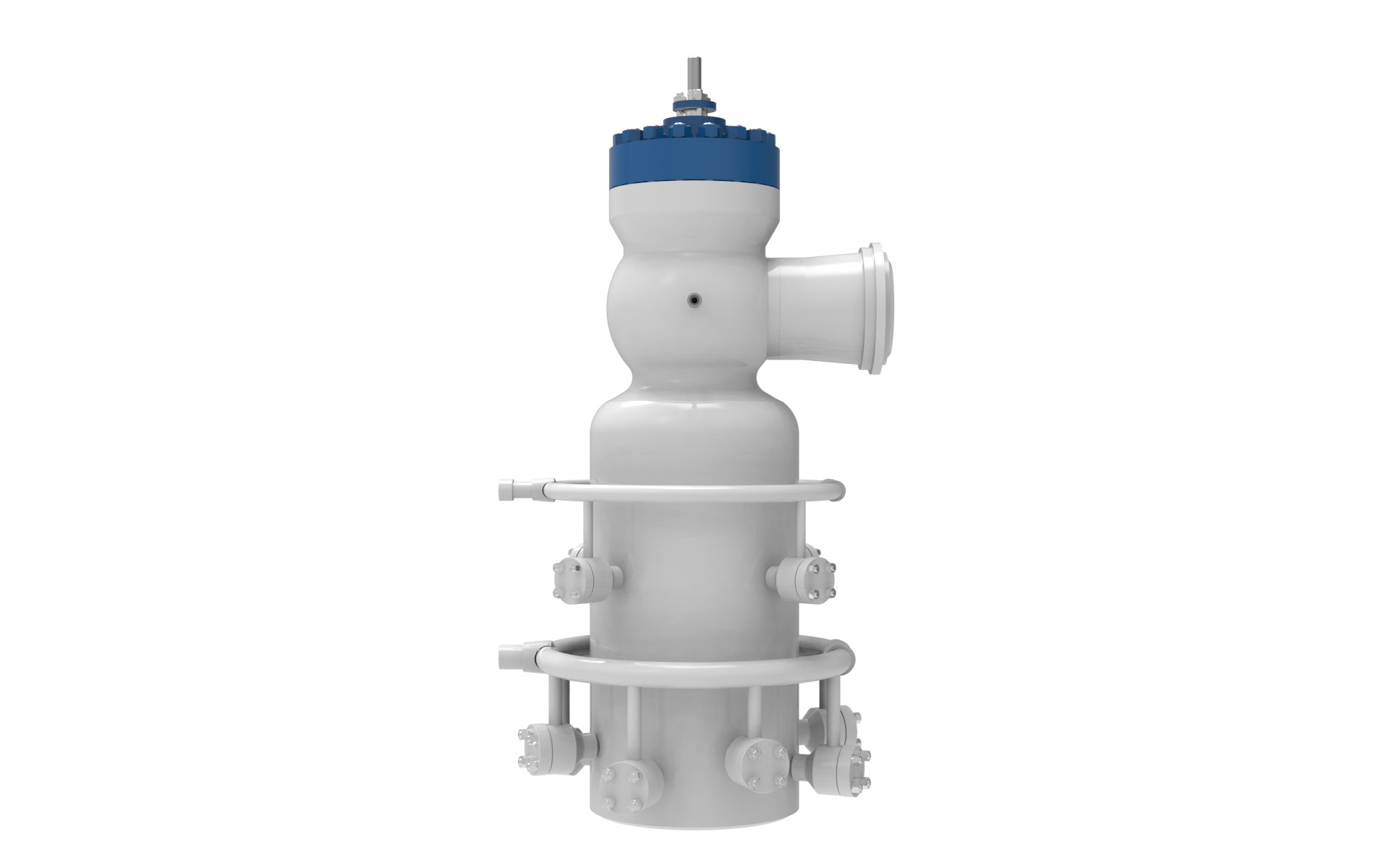
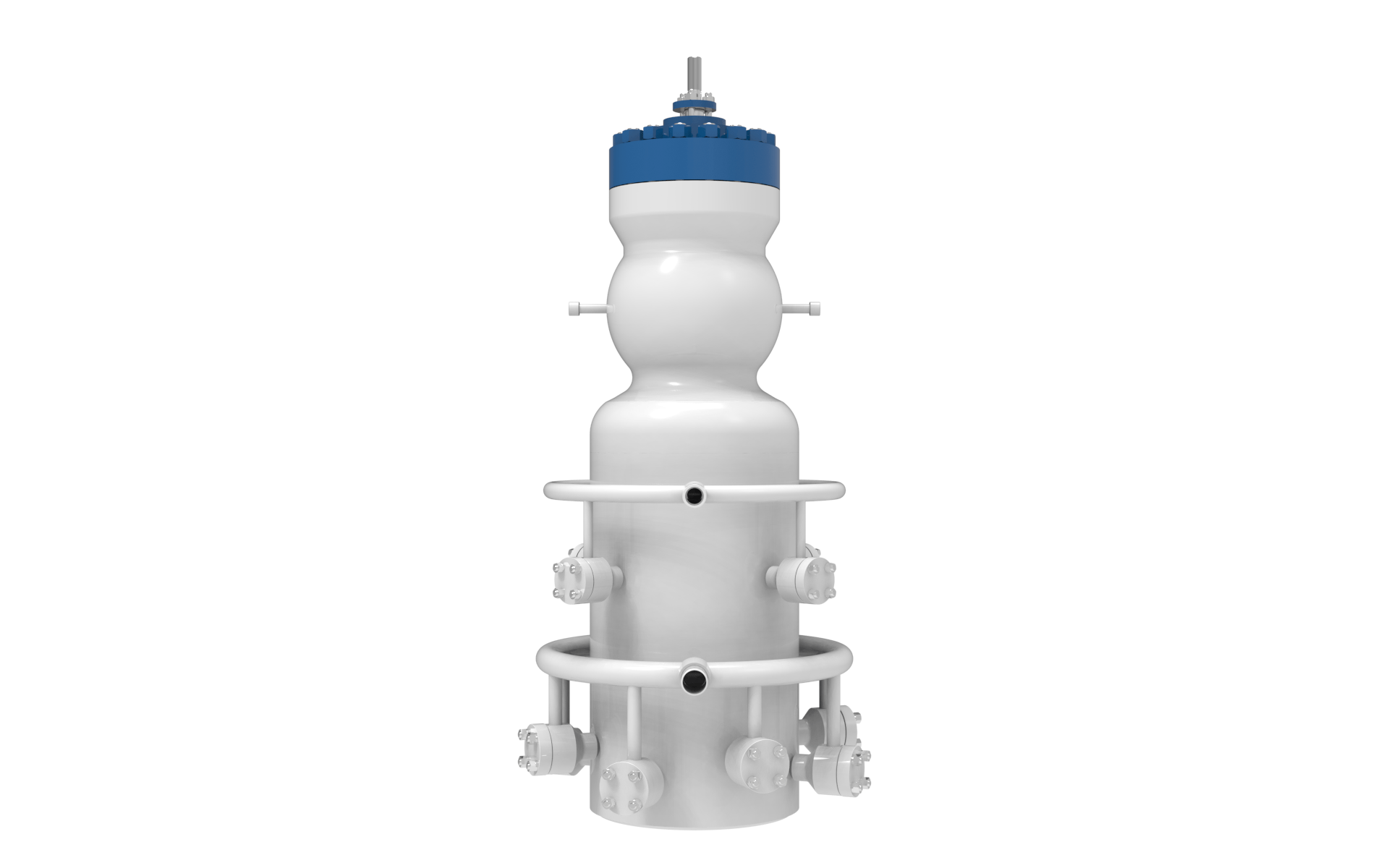
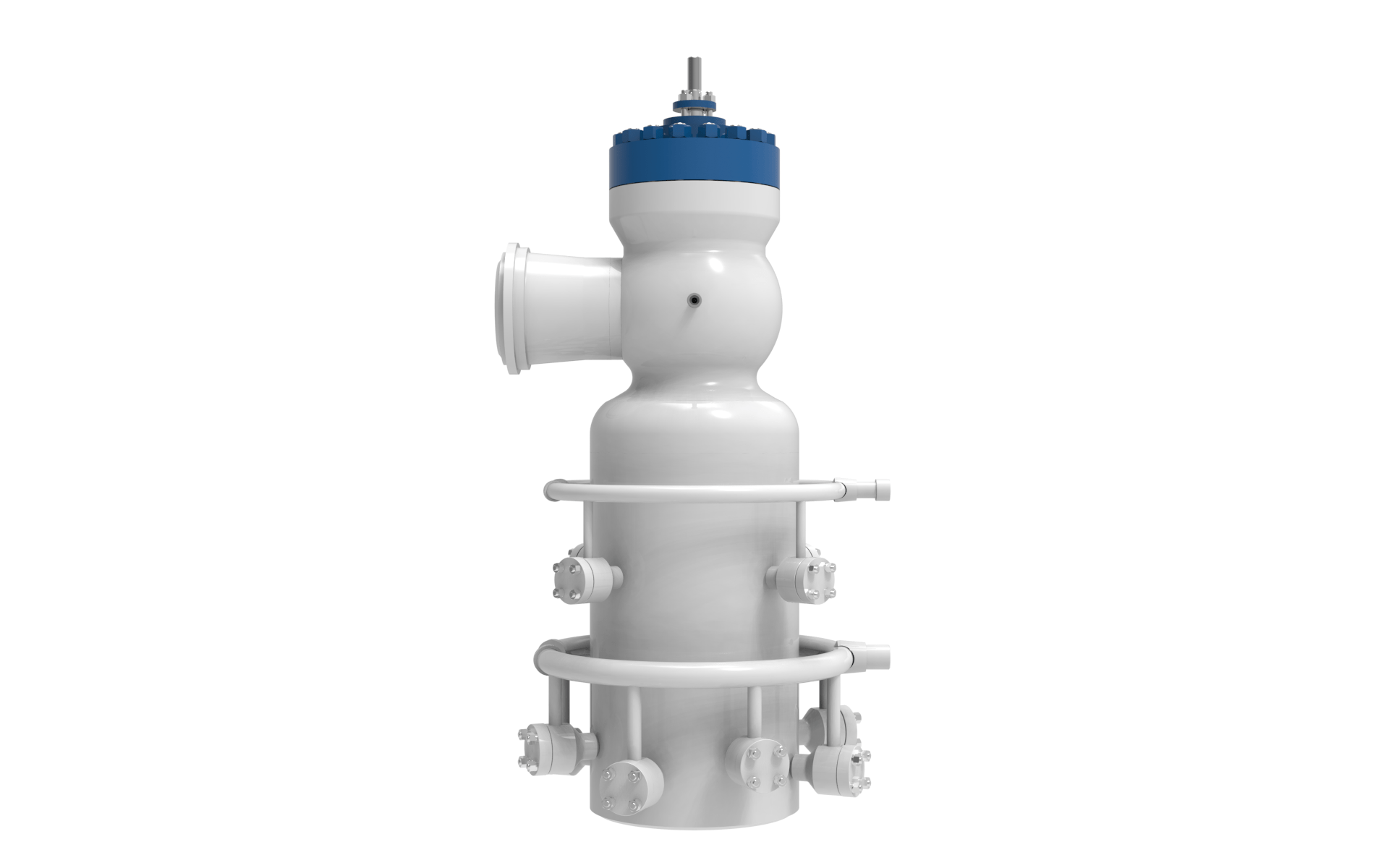
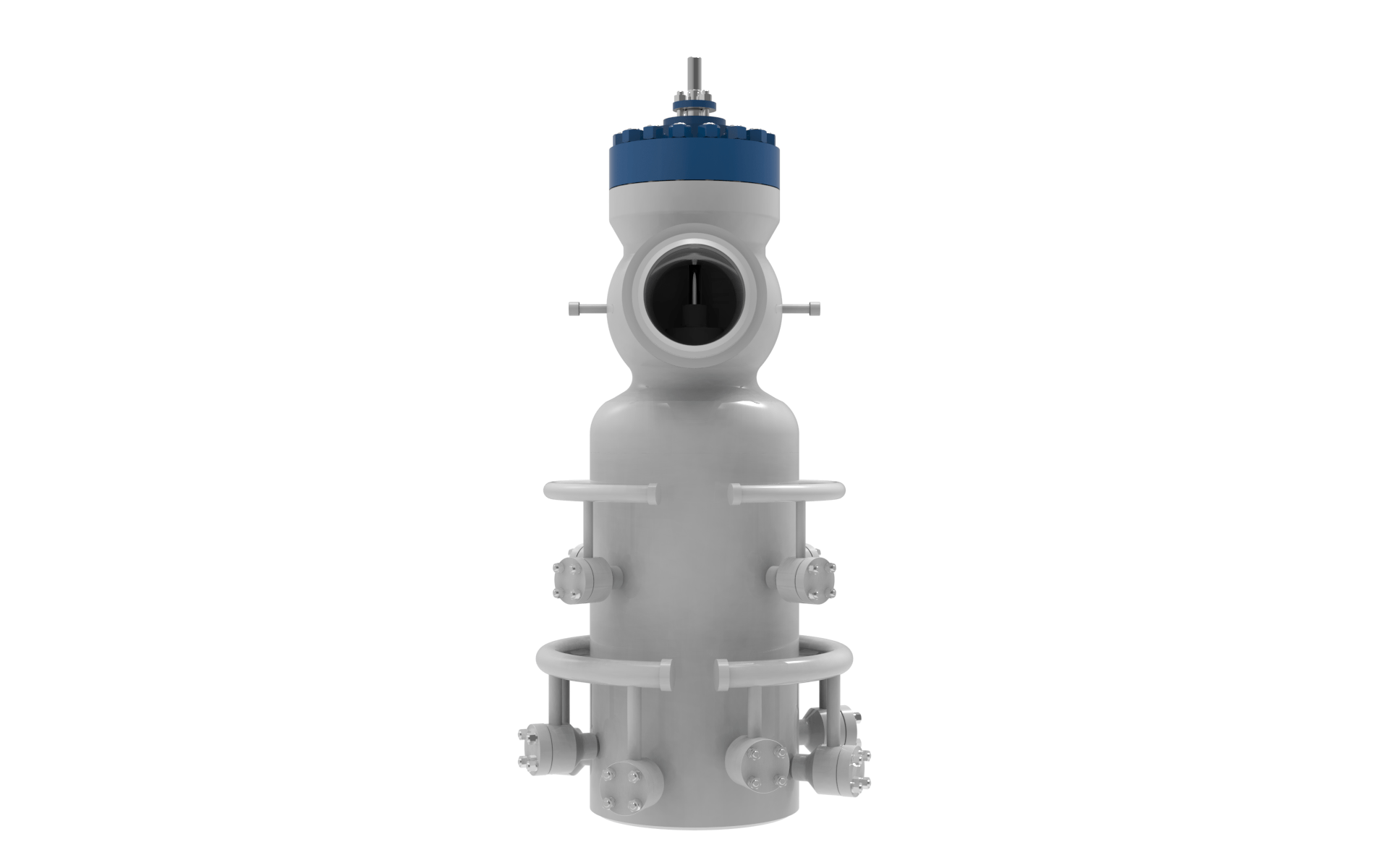
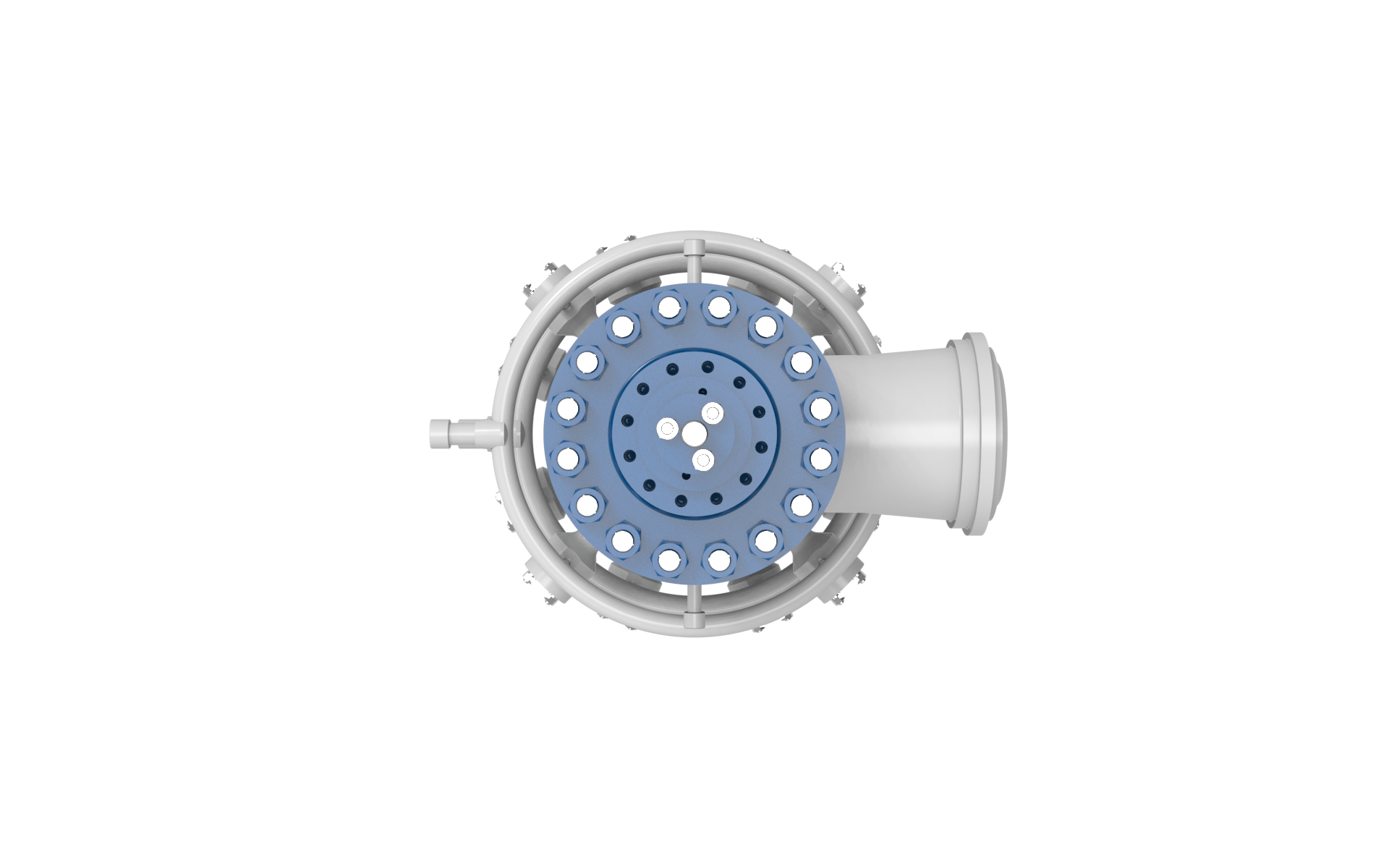
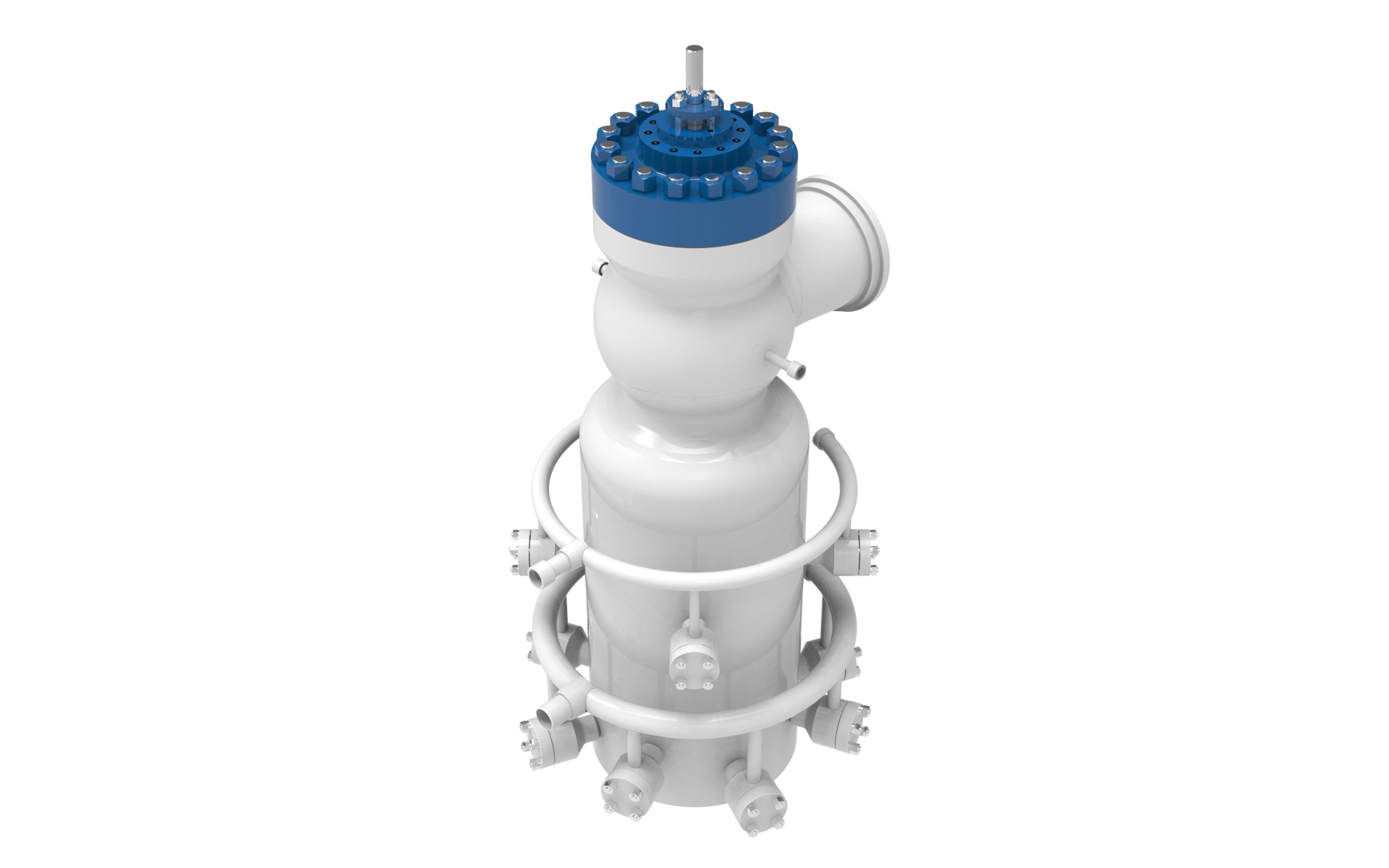
Blakeborough®
BV994/995 Turbine Bypass Valve
Conceptually, it is required to accurately control multiple operational variables, provide system protection to both upstream and downstream plant components, and sometimes, perform these tasks all in a fraction of a second.
Depending on the overall system size, bypass mode of operation, and customer preference, there is almost an endless selection of options and configurations that can be applied to the BV995 bypass valve construction. The Blakeborough® BV995 Turbine Bypass valve design can be varied to accommodate the particular plant design, size, and application. It is available in a range of options and configurations to assure optimum performance regardless of the mode of operation. The high pressure bypass valves are subject to some of the highest pressures and temperatures. They may be utilized in either a parallel or cascading bypass system.
PRESSURE BOUNDARY INTEGRITY
-
Bonnet closure provided in either a pressure seal (high pressure) or bolted (low pressure) design.
LOW STRESS CONFIGURATION
-
The inside and outside body contours are fully machined to assure a smooth transition with little or no stress due to thermal or mechanical loading.
CUSTOMISED DESUPERHEATING
-
The size, number, and location of the spray nozzles is optimized for each application to achieve the most advantageous distribution and coverage of the flow stream.
NOISE ATTENUATION
-
Pressure reduction is accomplished via two coordinated control surfaces and one or two outlet diffusers. Pressure reduction ratios are balanced to eliminate unwanted noise and vibration.
COORDINATED CONTROL SURFACES
-
Trim provides a minimum of two stages of coordinated control and pressure reduction thus lowering noise and providing excellent rangeability.
LOW NOISE TRIM
-
Three stages of expansion controlled trim provide a solution to meet noise specifications.
DESIGN STANDARDS
-
ASME B16.34
DESIGN RATINGS
-
ASME Class 150 to ASME Class 4500
-
PN10 to PN640
MATERIALS
-
Forged Carbon Steel (A105)
-
Forged Chrome Moly (F11, F22 , F91, F92)
LEAKAGE MINIMIZED
-
Available with three different plug configurations including pressure balanced for Class IV and Pilot balanced/unbalanced for Class V.
FULLY SERVICEABLE TRIM
-
Seat ring and pressure reduction stages are fully removable for service or modification.
VARIABLE GEOMETRY NOZZLES
-
Spring-loaded, backpressure activated, variable geometry nozzles provide an excellent spray pattern for quick mixing and evaporation.
WATER INJECTION
-
All desuperheating is conducted after the pressure reduction is complete, assuring little or no thermal shocking to temperature sensitive trim.
HARDENED SURFACES
-
All seating and guide surfaces overlaid with alloy 6 material to provide smooth stroking and tight shut-off.
TRIM ARRANGEMENT
-
The selection, number, and nesting of the appropriate pressure reduction stages is optimized to achieve a balance in the pressure drop ratio across the trim assembly and minimize noise and vibration. The plug has a single flow coefficient per valve size, the second stage has five different capacities, and the third stage has ten different capacities. In this way, they can be mixed and matched to achieve maximum stability and control.
SIZE RANGE & DIMENSIONS
-
Inlet – 40mm to 500mm (1 1/2′ to 20′)
-
Outlet – 40mm to 1000mm (1 1/2′ to 40′)
TEMPERATURE RANGE
-
Up to 650ºC